I enjoy working on projects alone. I like the peace and solitude. But not all projects can be done alone. It takes two to tango. Often I find that these multi-player projects involve metal. Here are a few metal collaborations I’ve been a part of or witnessed.
In my junior or senior year of high school I had a friend who had a somewhat messy home life. Let’s call him Kyle. Kyle was a friend who would often come over and play video games (LAN parties, not really the same in 2023 I’m sure.) Kyle was similarly nerdy and we’d read similar books. I don’t think he was that interested in Dungeons and Dragons like other nerdy friends, but it’s possible I just forgot his typical characters.
I don’t really know how this all went down, even after Kyle explained it all there were a lot of questions that I never really had answers to. He was home playing video games, maybe counterstrike 2, and for some reason his step dad was messing with him. Kyle tried to blow off his step dad but at some point his step dad cut the power off at the breaker and Kyle knew that it was time to act.
Kyle went to the kitchen and got a kitchen knife. He had to be ready. He left the house and went around the side to confront his step dad. His step dad had picked up a chair; the chair was a weapon to hit Kyle. But Kyle had his piece of metal, and plunged it into his step dad’s side. It takes two to tango.
I told my wife this morning that fifty percent of woodworking is devising faster and strong ways of holding work still. One of the oldest kinds of clamps is called a holdfast; it’s a big piece of iron meant to clamp work to the top of a workbench. Holdfasts can be expensive; ordering a high quality one from the internet can exceed $100.
Historically a holdfast would be forged by a blacksmith. You can buy forged holdfasts from etsy today and I have only heard good things about them. I have a friend who does blacksmithing as a hobby and I decided to see if he was interested in collaborating on a holdfast. I drew up some plans (based on the crucible holdfast linked above) and ordered the iron. He did the smithing to get it into shape.
After Pierre delivered the first holdfast, I made sure it would work. If you do research online you’ll see that some holdfasts don’t work in a workbench that is too deep. My bench is 6” deep, which is about as deep as I’ve ever seen. I got some random dimensional 4x6 material and bored a hole in it, and then tried to bang the holdfast home.
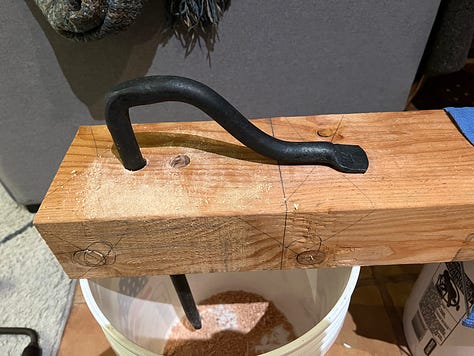

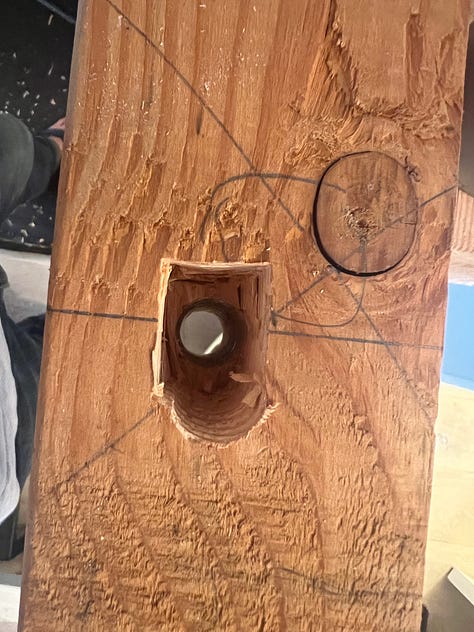
It worked like a champ. I think the main thing I had to do was bore a 1-1/8” hole, despite a 1” hole theoretically being sufficient. I don’t know if this is because the holdfast was ever so slightly too wide or because I did a bad job boring a straight hole, but that’s not too much work.
After verifying how to make working holes, I planned where I’d bore holes on my workbench. I find putting holes in my workbench somewhat harrowing and stressful. It shouldn’t be so stressful but it is, so I drag my feet on doing it. I bored five holdfast holes about 18” apart from each other. I did it with a spade bit and a brace, so it was pretty brutal work, but the result is so useful that I regret none of it.

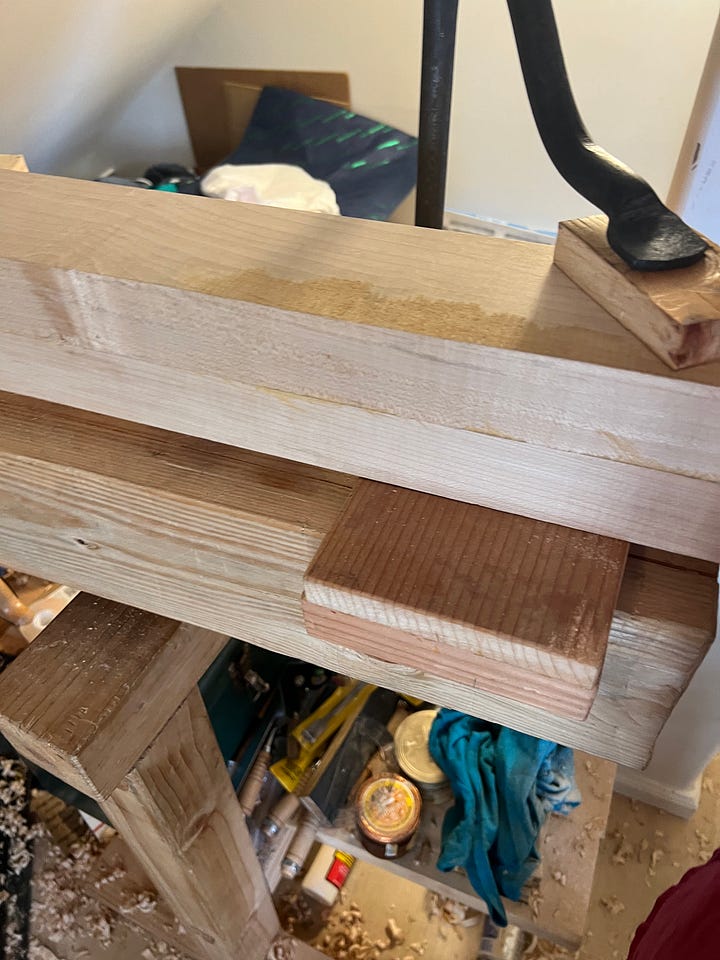
I still need to add more holes at the front of the bench, and some slots somewhere to store the holdfasts…
Another major workholding tool that I lacked was a planing stop. A planing stop is basically a set of teeth that bite into wood to keep it still while planing. Often the planing stop is movable, such that you can have it a mere 1/4” off the top of the bench, or as high as 6”. You slide a piece up against it, it bites in, and you get to planing.
I could have ordered one of these, but again, having it forged is cool and collaborating is fun. I would have reached out to the same person that did the holdfasts, but we don’t see each other as often, so I tried a different tack. I have a friend (who I’ve not yet met in person) who does blacksmithing in Texas. I decided to draw up some plans for a planing stop and see how that went.
While he was working on the metal part, I went ahead and made the slot and moving wood portion for the planing stop. I got some of my random 4x6 Douglas Fir and crosscut a piece to about a foot long. From there I marked it up to be about 3-1/8”x3-1/8”, and ripped it to that size, with the intention to plane it to size once I have the matching hole done.
I marked up the hole in the bench at 3”x3” and got to chopping. This is a deep mortise, a full 6” deep. If I were conserving my energy I would have bored most of the waste out before chopping, but I wanted to get the energy out so I only chopped….
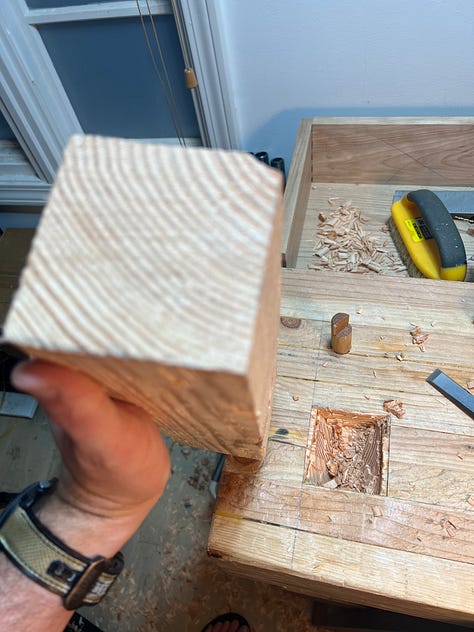
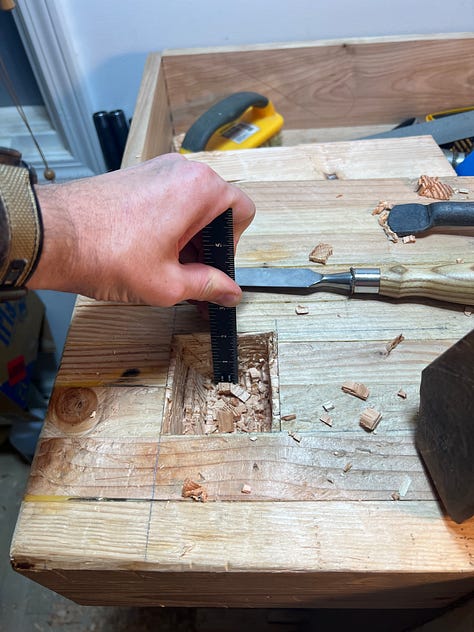
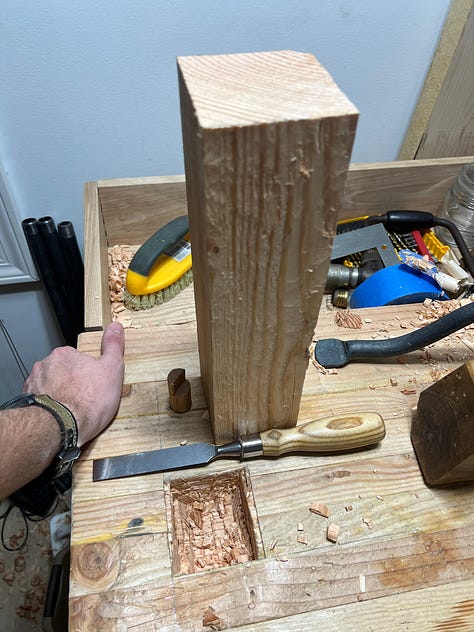

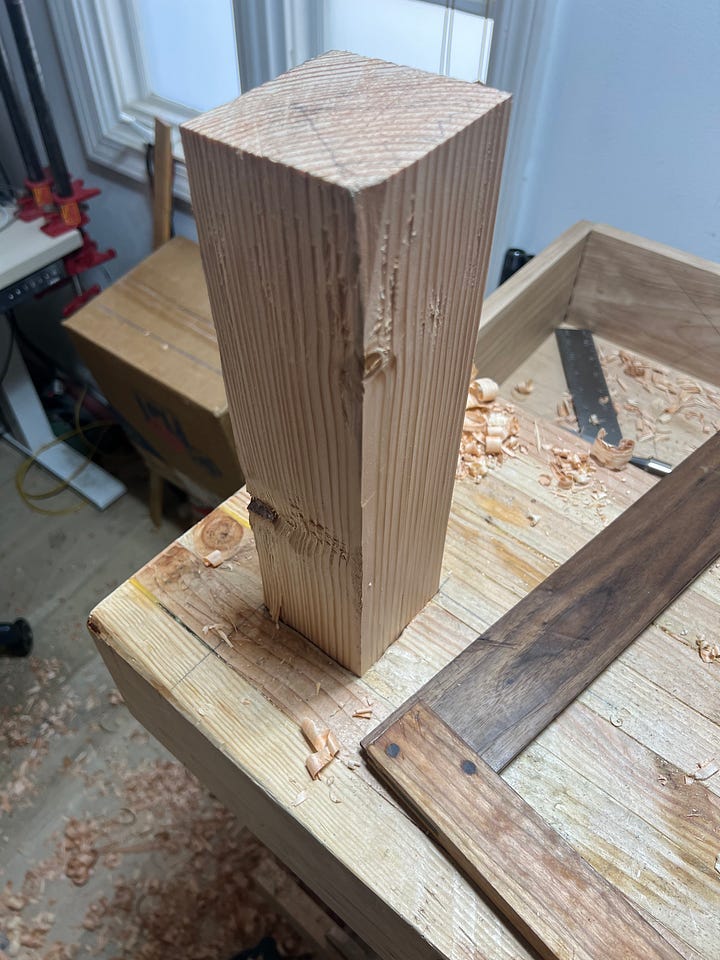
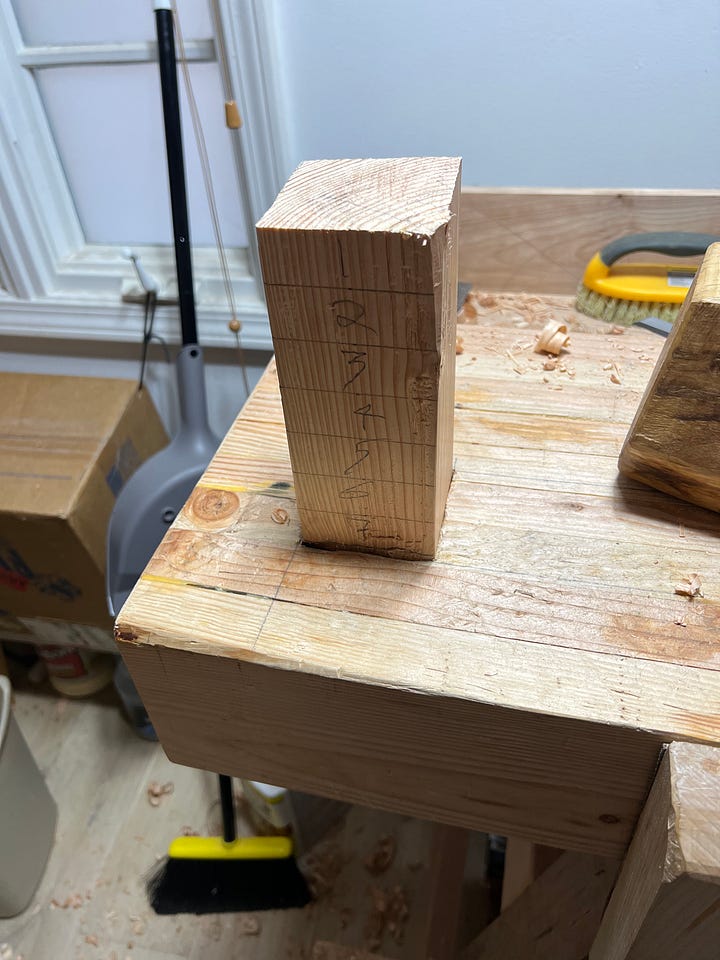
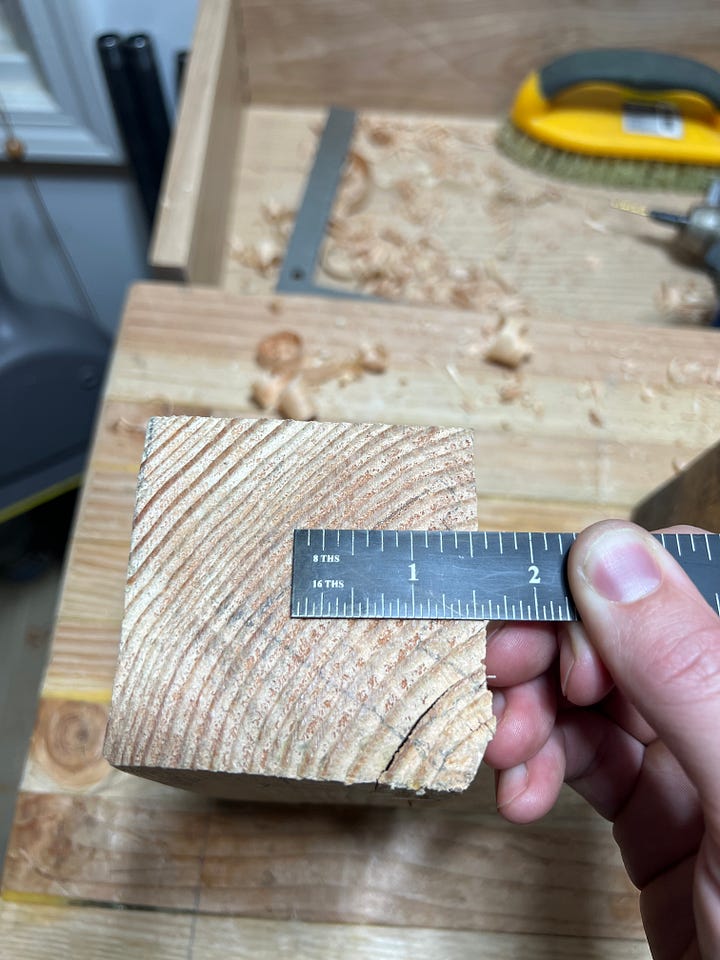
Here are pictures Eric took of the holdfast before sending it:
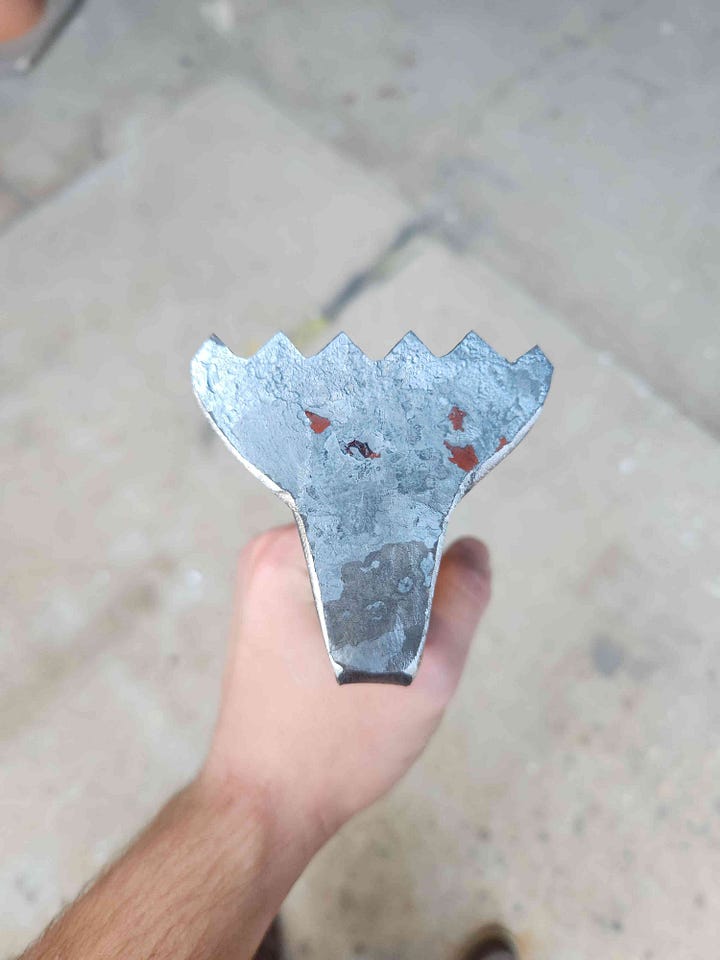
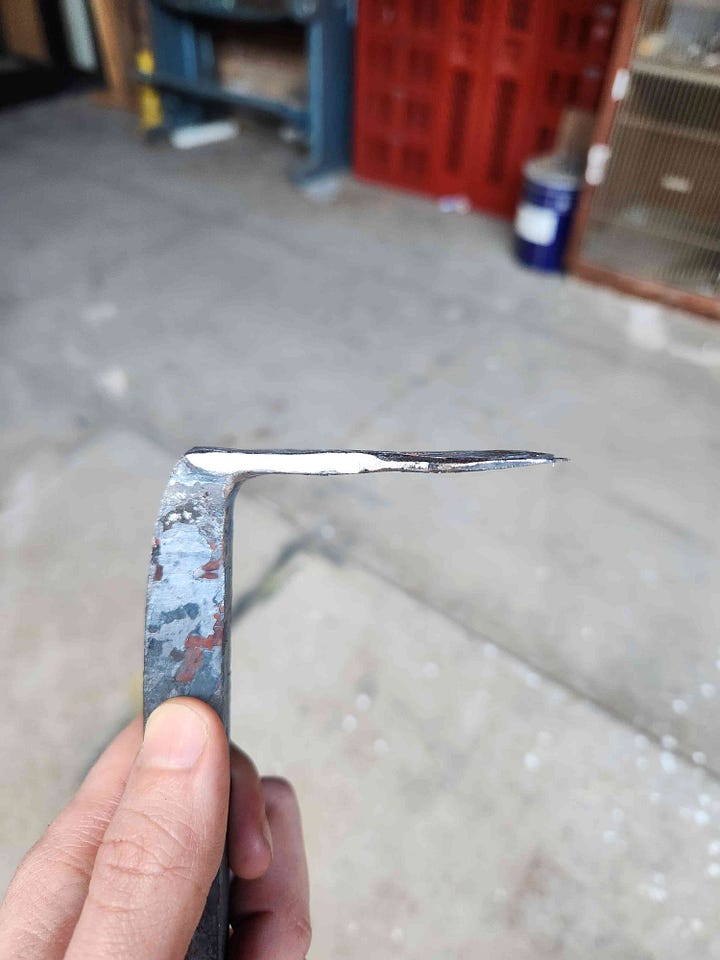
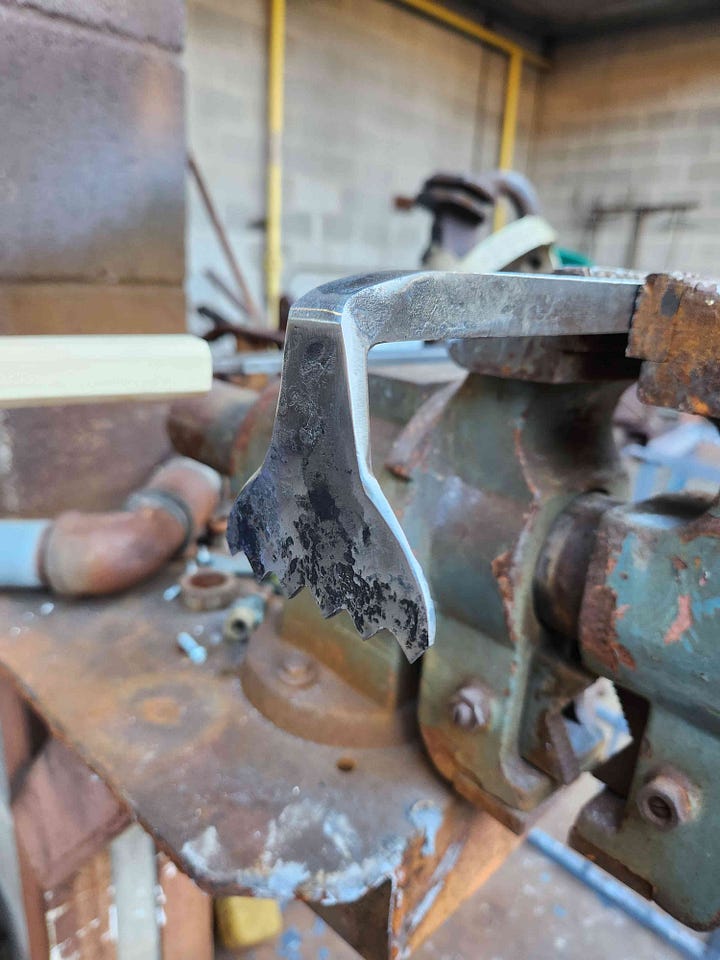
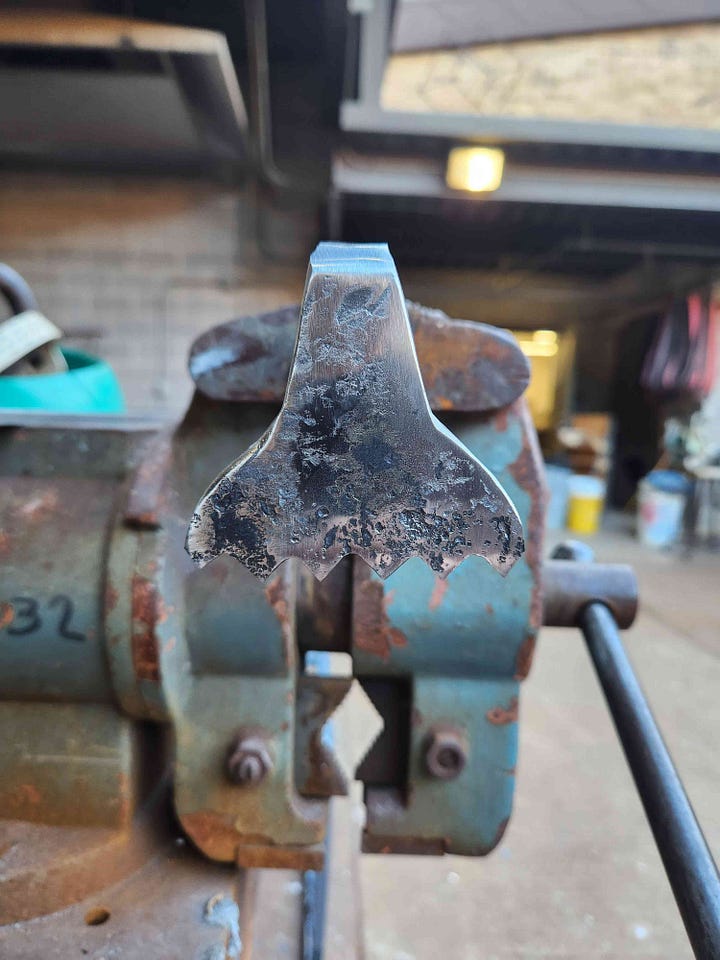
To embed the planing stop into the sliding slot, I needed to bore a 3/4” hole all the way through the foot long slot. I only had a 3/4” spade bit and it wasn’t even long enough to bore a 6” hole (which would then meet in the middle.) I bored 5” holes from each side, and then used a bit extender to bore the last two inches and meet in the middle.
Frustratingly the bit extender wobbled and ended up making a painful non-straight hole.
I eventually decided to buy a long (18”) auger bit in the hopes that it would allow me to connect the two holes…
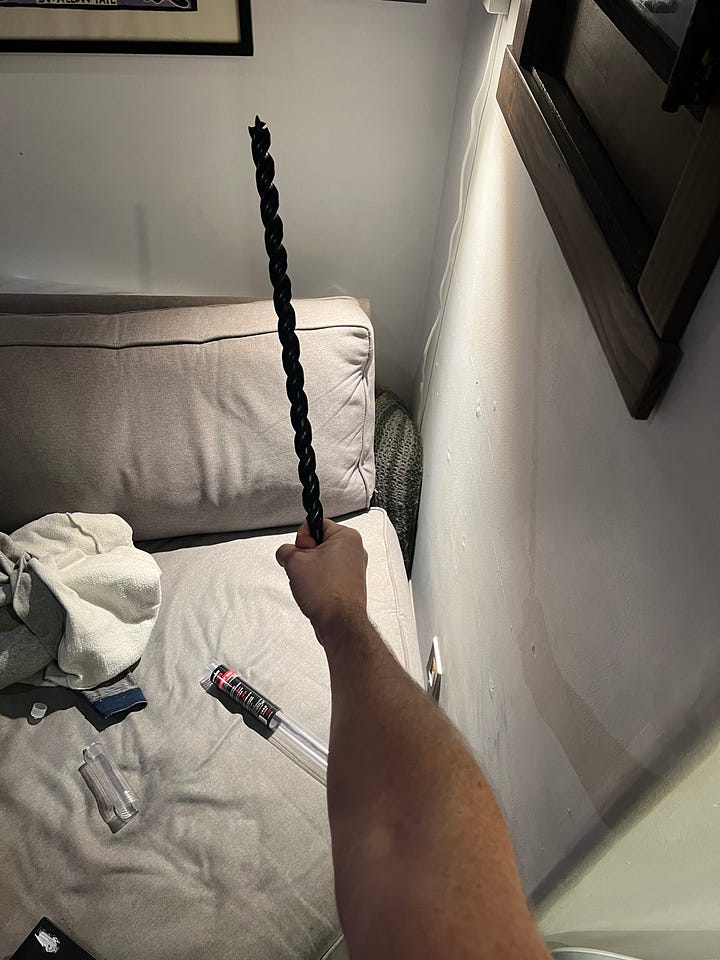
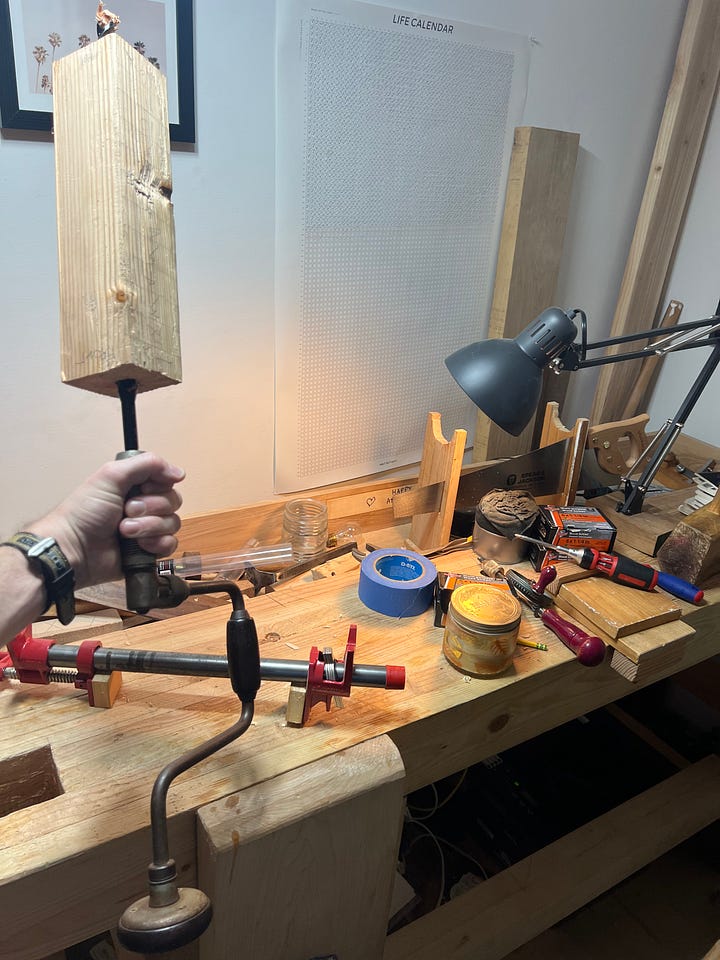
After that I pounded things into place.
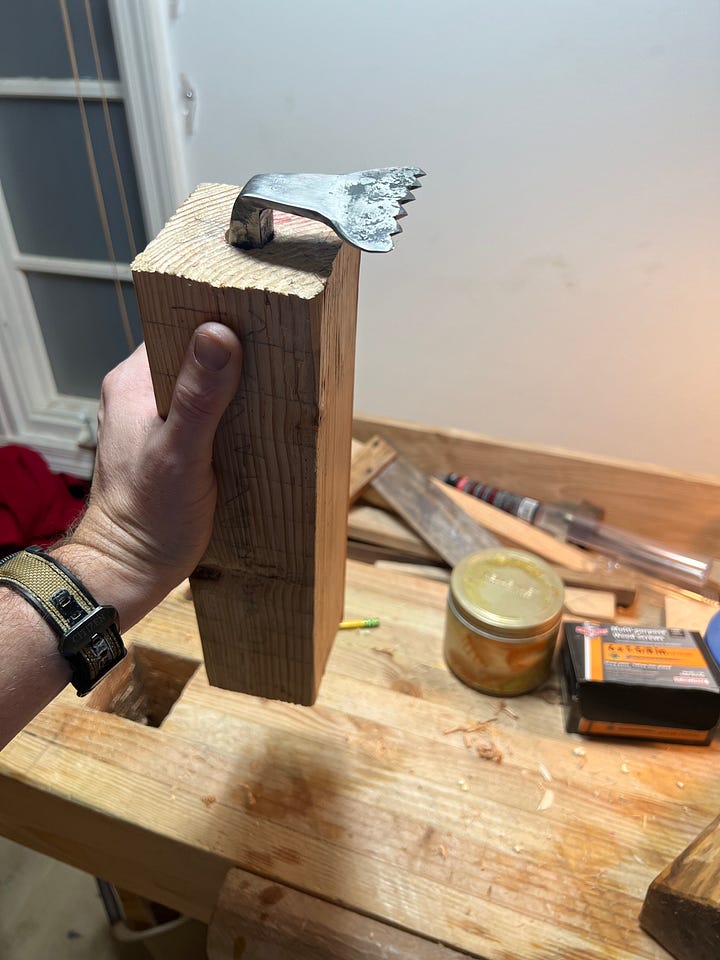
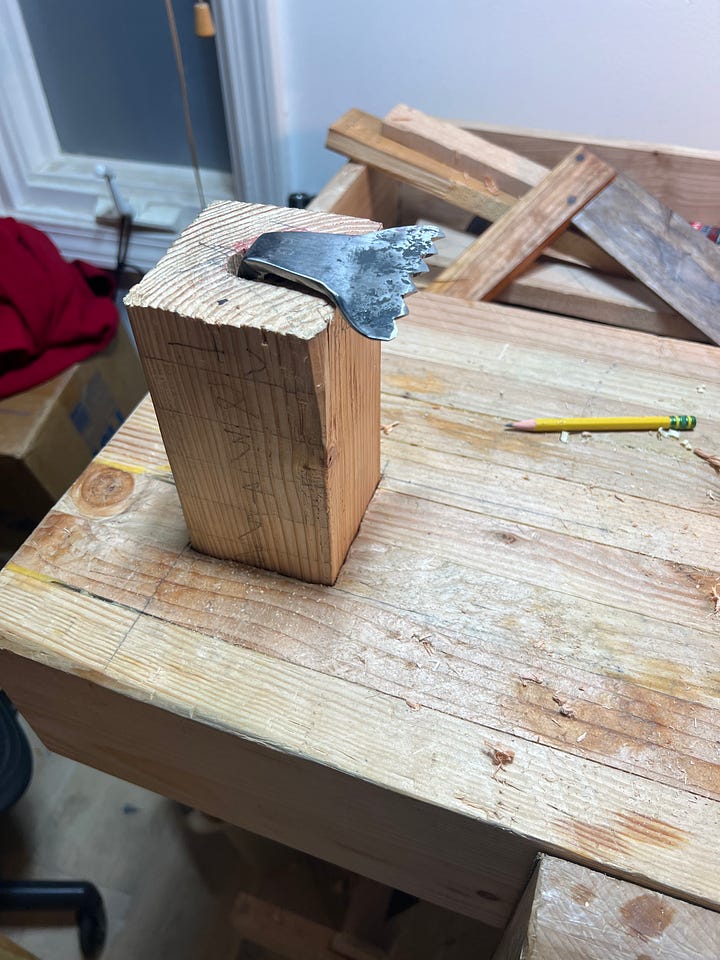
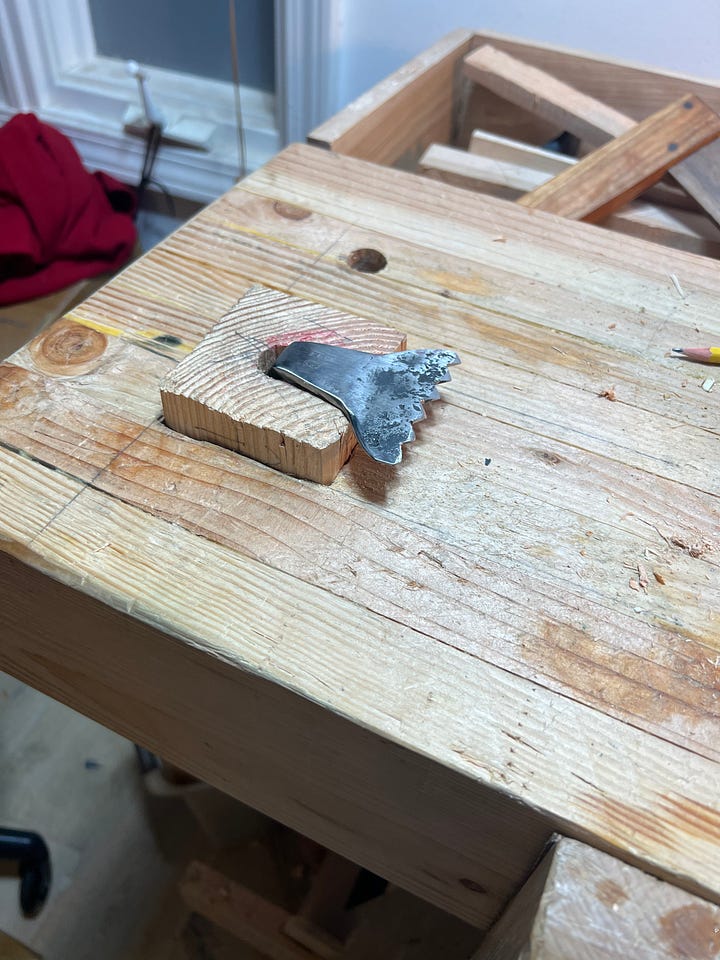
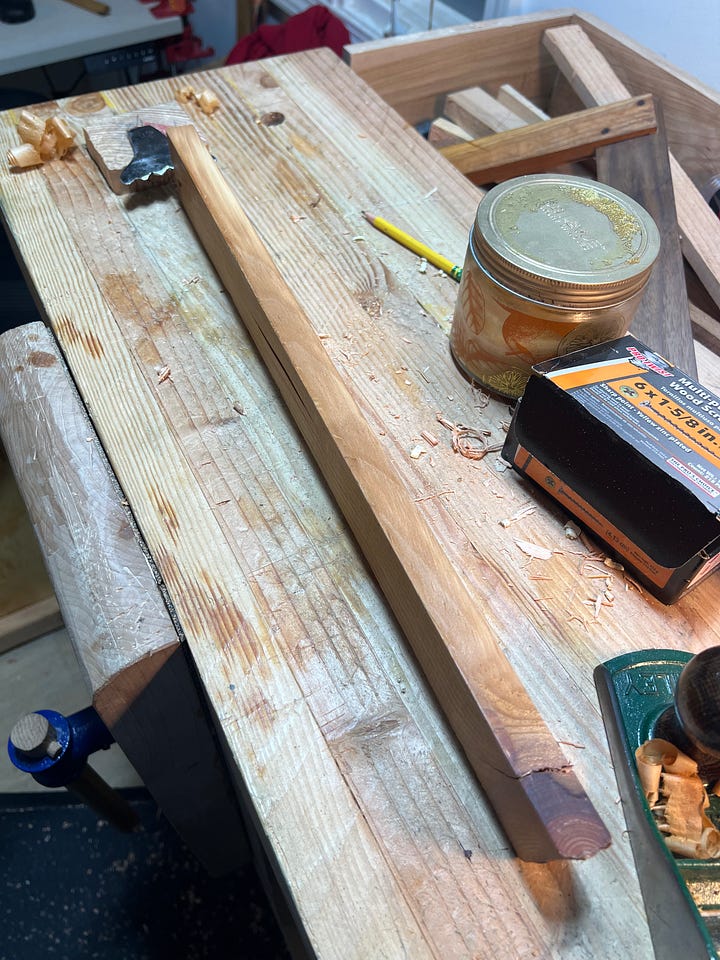
I have only had time to try it out for the picture above, but I am eager to use it more.
In 2003 I had a friend whose house got broken into. Normally when this happens, you come home (or maybe wake up) to a mess or a bunch of missing stuff. In this situation my friend was awake. He heard the person breaking in and defended his house.
My friend had his piece of metal and shot the thief while the thief was trying to get the front door open.
One of the weird subcultures I was a part of in high school was the punk rock crowd. These punks were extremely liberal and socially aware. One of them asked me how my murder tasted (a sandwich with meat on it.) I don’t think they were generally gun people.
This friend was part of that group. He felt bad! He went to the guy and asked him, “Are you OK?!” It takes two to tango.
Wait what? You didn’t finish the stabbing the step dad story!
I can’t believe how much work this woodworking is! And how much energy it takes, sometimes purposely! Are you still jogging?
I’ve been wondering about getting a holdfast for a while - but also wondering why they are so expensive - great piece Frew. Also - that planning stop is a rather more chunky version of what Rex Kreuger sells and shows on his videos - but I suspect not quite as expensive either. Will be interesting to see how you get on with both of these - I’m also tempted to find a blacksmith to make me a holdfast here in the UK