In the Summer of 2009 I was sitting on the front porch of our old house in Mississippi and telling my dad and my sister about my job. At the time I was working at a company called MTSI in Richardson, TX. Back then most of what the company did was contract engineering (both software and hardware.) The one I was working with did mystery shopping for apartments, to ensure that the people renting the apartments were doing a good job and following company policies. My dad didn’t believe me. He was confident I was some kind of spook.
Thirteen years later I’m dying to make progress making my bench. Avi suggested Japanese sawhorses, linking to this article from American Woodworker. I followed the article and a link (which I can no longer find) from Avi that showed the sawhorse made almost entirely from 4x4 dimensional lumber.
I made two of these sawhorses entirely out of 4x4 Douglas Fir I got at Home Depot. All of the sawing I did with a cheap hardened steel handsaw. The mortises were chopped with a Thorex 650g hammer and mortising chisels my inlaws gave me for Christmas.
The first sawhorse was made while my wife and kids were in Texas. I would chop mortises for hours on end in the living room during weekends, or evenings during weekdays. Ultimate bachelor mode is intense manual labor. I built these sawhorses with maniacal fervor.
I made plenty mistakes. I was going so fast it was inevitable. The biggest mistake was when I followed the American Woodworker plans, rather than the ones I’d written myself, and chopped a too-wide mortise.
The other big mistake I made was chopping the mortises in the top too far apart.
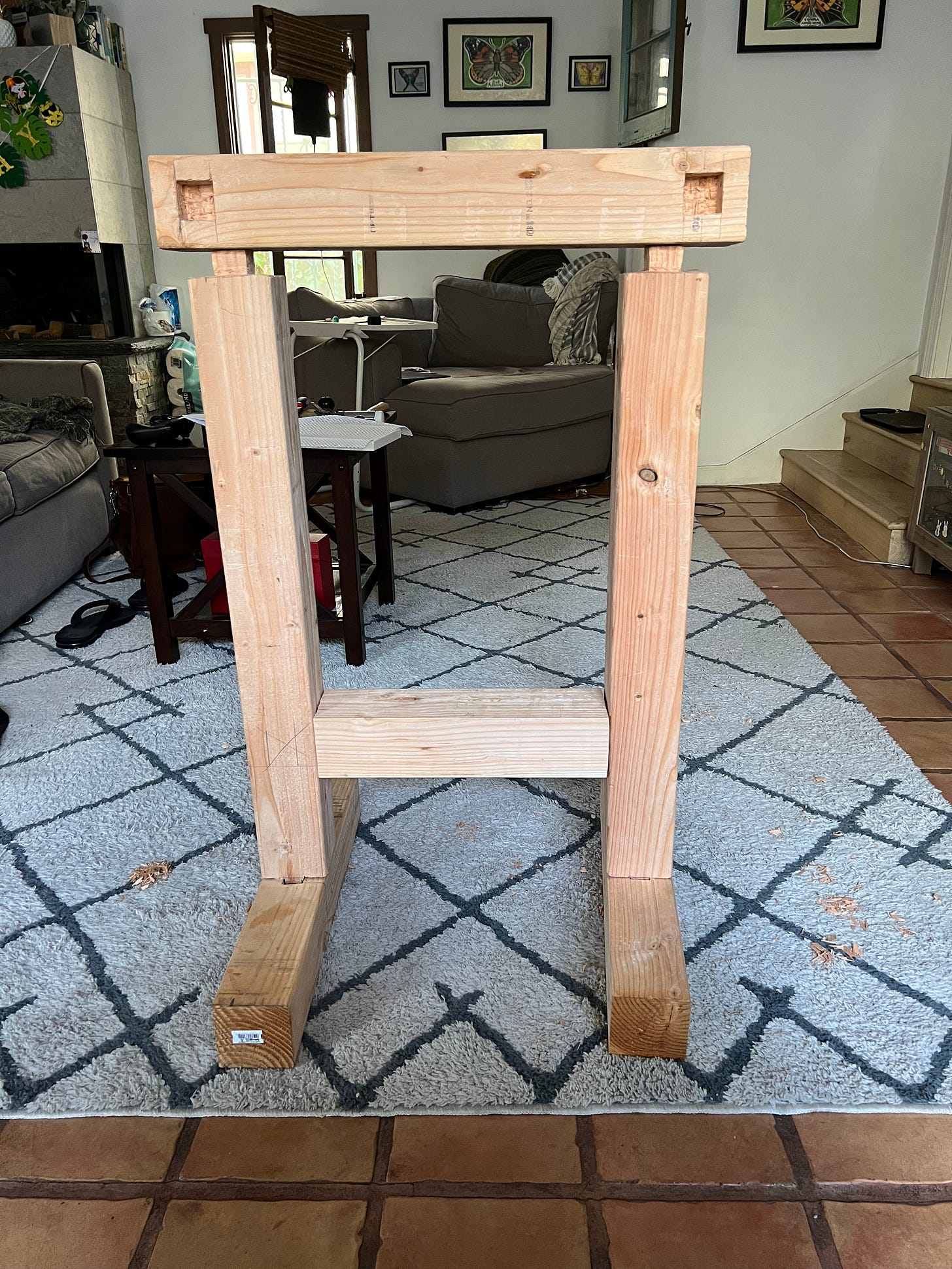
I fixed the first problem with wedges to tighten the tenon in the foot.
For the top I cut the existing mortises wider till the tenons would fit, then I added hardwood plugs to trim it back down to size.
Using the first sawhorse to build the second one was satisfying. I could clamp work to the sawhorse when sawing and chop a mortise standing up straight. Before that I was chopping mortises at my desk.
The sawhorses became a transitional undercarriage for my bench until I made the final undercarriage.
If I had it all to do again I would have done only a few things differently.
I would have invested in better saws much sooner. Rip saws are surprisingly expensive, but a good crosscut saw can be gotten for less than $50.
I would have made the stretchers use tusk tenons rather than wedges. The current assembly is effectively permanent.
I would have made long stretchers between the two sawbenches to make them more stable for the benchtop.
I would have added dowels to the tops of the sawbenches to fit into the bottom of the benchtop (we’ll see that in a couple of days) so it wouldn’t slide as much on top.
Back in Mississippi. Near the end of the conversation my sister Tara asked, “Art, how much do they pay you?” I’m sure I made some kind of uncomfortable face. My dad was aghast and said, “Tara! You can’t ask that! That’s like asking a man how many horses he has!”