When I lived in Texas my friend Melinda baked the best cookies I’ve ever had in my life. Oprah liked these cookies. I think there was something about these cookies being at a football player’s wedding. They were really good. I wish I could have one of those cookies right now.
I remember when we’d get together on Monday nights she’d often (always?) bring a dessert and she was never happy with it. She always had ideas of how they could be better and asked for suggestions or critiques. I didn’t like that, I told her they were great and she should feel good about what she’d made!
But I was the confused one, not her. You don’t get to the point where you make the best cookies West of the Mississippi by being proud of what you made: you get to that point by never accepting that what you made was good enough.
When we moved into our new place, the previous owners left a significant portion of their furniture behind. This seemed like a good deal; free furniture! But as we settled in I came to the conclusion that most of this designer furniture made sense to leave behind: it wasn’t good.
The coffee table they’d left behind was a plain glass topped thing. I hadn’t planned to replace it, but my boys would stand on it and I could see the glass flex. I told them to stay off the table and then got to work replacing it.
I designed this new coffee table. The engraving was inspired by Schwarz’ American Peasant. The functional design was informed by Lon Schleining’s Treasure Chests. It took me about four months to build. Here it is.
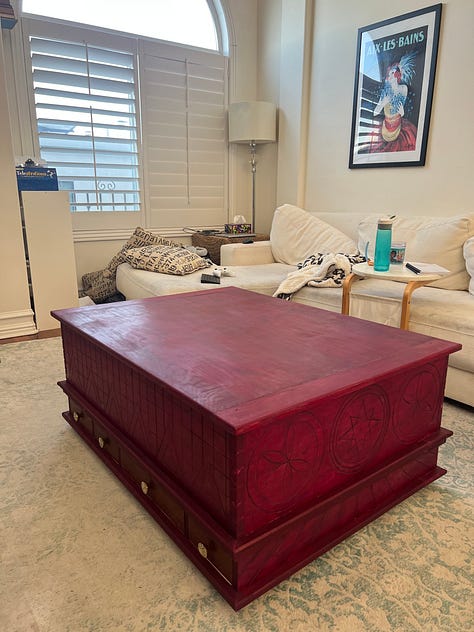
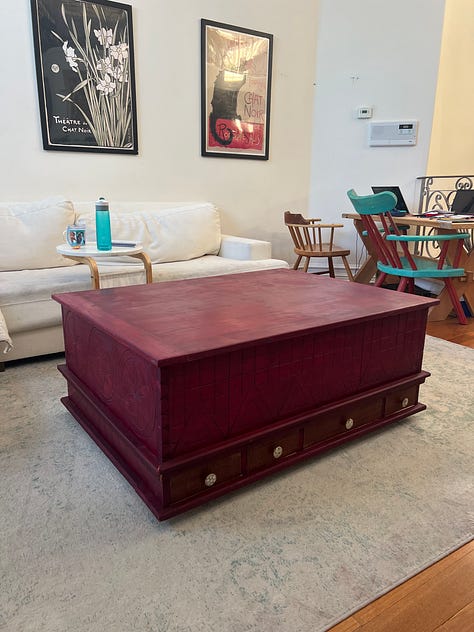




New to Me
I attempted many new techniques in this project. I read that in the UK they finish before assembly, rather than after. I tried that with this project, because the engraving would be much more difficult to do after assembly. It worked out but there were a few issues:
The clamping marred the soap finish.
I was hesitant to paint the dovetails before glue up but that added extra annoying steps, I should have just painted those before. I was worried BLO or soap would interact with the glue, but I could have just left those two parts off of the tails, or done a test.
Painting while basically laying on the floor sucks.
Usually when I build a piece I complete it in my shop. This time I assembled it in its destination so that I wouldn’t have to carry it up multiple flights of stairs. It worked out, but it was obnoxious to have a tarp, wood chips, hide glue, and drying paint in my living room. I don’t regret it though.
This was my first project that featured moulding. I have made and used moulding once before, but that was just replacing existing moulding. This time I did it because my wife asked me to, to protect the softer wood, and to cover up unsightly joinery. Moulding is not really fun to make (for me, currently) but the end result looks great.
This project features drawers. That meant learning to make half-lap dovetails.
I used some lacewood my wife got me for our anniversary for the drawer faces. It’s pretty but fragile and unpredictable. I wouldn’t use it again.
Also with the drawers I basically used the wood for the drawers as is, so the sides and bottom are 4/4. Very chunky for a drawer. If I did it again I’d plane the sides to 1/2” and the bottom to 1/4”.
The lift top lid was a first for me. It should lift 100lb and it holds the top nicely. While moving it’s somewhere between nerve wracking and terrifying. The top doesn’t lift up level but instead twists. I don’t know if this is because of length of the lid or the width or the cheapness of the hardware or what. The way the lid works is the biggest disappointment in the final piece for me.
The engraving was fun! I am very pleased with how it looks in the end, and it is relatively easy to do.
I planned to purchase feet but had trouble finding any that met my needs. I wanted them to be low profile, easy to slide, attachable to the bottom without interacting with the drawers. I enjoyed designing, making, and attaching the feet for this chest. This is one of my favorite features of the chest and almost no one who sees it will ever know.
Mistakes were Made
The most significant mistake is the joinery for the bottom. The bottom is kept in place by a groove on the left, a groove on the right, and one nail per groove:
In theory it’s also held in place by nails for the moulding and the drawer separators, but I am nervous about depending on those. I don’t know what I should have done instead, and it still looks ok, but I’m nervous about this joinery.
It’s basically all one color. The different woods used in the project offset the colors slightly, but if I did this again I’d probably make the trim be a different color, likely a bright yellow. Multicolor designs are risky, but I think they are very much worth the hassle and stress.
The rest of the mistakes mostly meant that the final product took longer to build, rather than affecting the outcome.
I didn’t make enough moulding. When nailing on the moulding I discovered that the moulding I’d made was too short. I ended up needing to make more moulding that didn’t perfectly match the previous moulding, required another round of nailing, etc.
I didn’t shoot the end grain of the dovetailed boards. I am skeptical that every corner needs to be perfectly square, but shooting the end grain would have meant I didn’t need to do as much sanding.
The dovetails were too wide. Because of this they were fragile and I needed to patch gaps where the corners broke off. Were I to do this again I’d use shallower dovetails for the basswood.
While nailing on the moulding I ended up tilting one of the pieces of moulding maybe 2°. It’s pretty subtle to most people but it’s obvious to me and drives me crazy. To avoid this I should have made a line to follow.
Similar to the moulding being wonky, some of the engraving I accidentally rotated very slightly over and over such that the engraving at the left is plumb and the engraving on the right is tilted a little bit.
I wanted to finish the top with shellac, but (after purchasing the shellac flakes) I discovered that purchasing denatured alcohol (required ingredient in shellac) is fully illegal in the state of California. I think I might try using high grade ethanol at some point, which I can find, but is pricy. Or just buying it in another state.
I don’t know why I was so confused when I talked to Melinda about her cookies fifteen years ago. At the time I was very driven and even perfectionist when it came to writing code, but for some reason I couldn’t understand that in this case.
I get it now Melinda. People see my chairs and my coffee table and they say “this is amazing!” and I say, “it really isn’t. It has dozens, even hundreds, of problems.” They tell me I’m being too hard on myself. They don’t get it. I don’t want to make a good enough chair, I want to make a better chair than I made last time. I want to use new techniques. I want to build faster. I want to build cheaper. I want pieces to be lighter and better and more beautiful.
But moderation in all things. I strive to improve, but I am proud of what I’ve made. I am pleased with the outcomes and I enjoy the process. I am aware that what I have built is good enough, and I am also aware that what I have built has a lot of room for improvement. I seek out what could improve. I write it down. I do better on the next one.
I can’t wait to meet this blanket chest! If it were smaller or we lived closer, I’d commission one. Love it.
Brother, you already know how impressed I am with this table/chest. Your right about the hinge. I hold my breath every time I watch your video of the finished install. I think the twisting is all on the hinge. I don't think there's anything you could do to correct it.
Take a shot at a scaled down version for practice & maybe try pistons for the assist, though those come with their own problems.